Nomad
From the 1967 STAR TREK episode "The Changeling"
In 2017 I was asked by hyper-realistic painter ADAM ROTE to create a 1:1 sculpture of the Nomad probe to display at an art gallery show on science fiction pop culture that he was organizing.
The original prop was, no doubt, cobbled together from inexpensive and easily obtained objects available in the 1960s. However that was not the case in 2017! So I knew I would have to build almost every single piece from scratch.
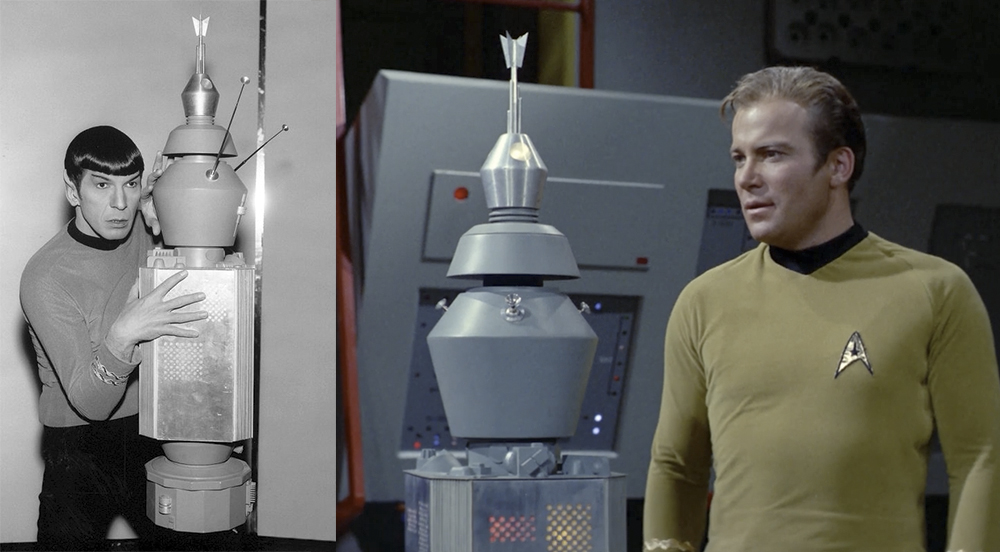
Design and Planning
I initially found some very good fan blueprints online, but since I had to engineer the parts break-down and draw vector files for the laser cutter anyway, I ended up spending around 300 hours researching and drawing my own plans.
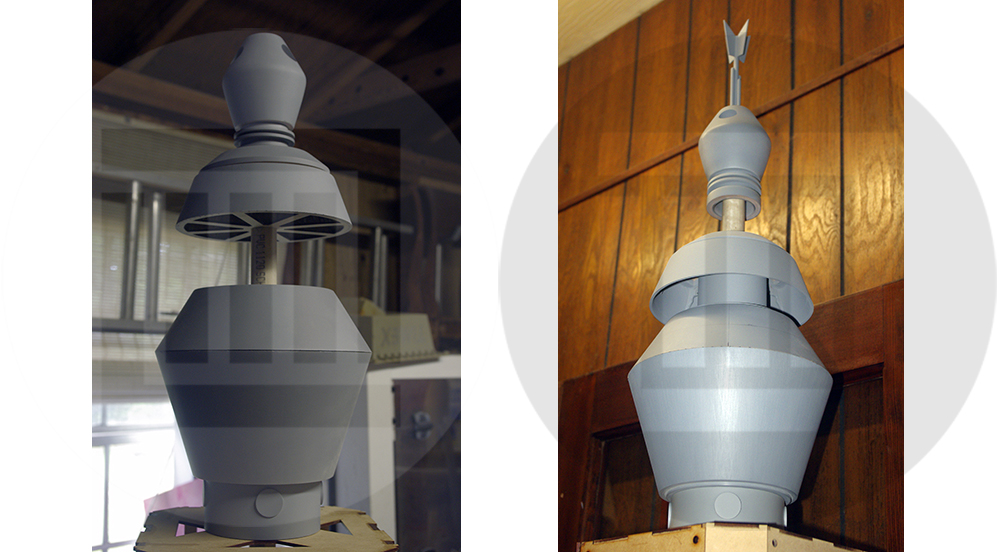
Construction 3
I glued these outer skins over inner supports and coated the insides with fiberglass resin for strength and rigidity. Then I coated the exteriors with Bondo filler. Once dry, I removed the internal supports and sanded everything smooth.
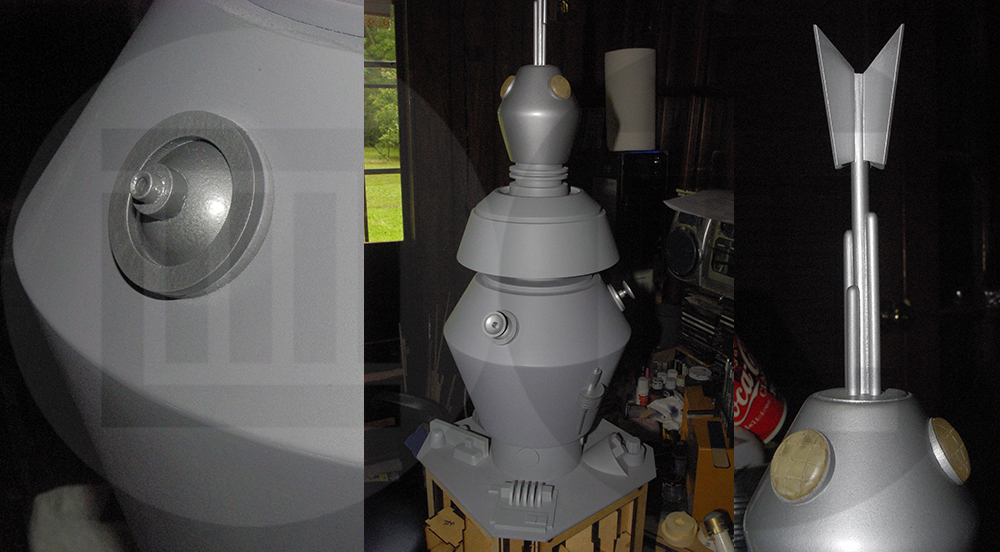
Fine Details
I hand-sculpted the detail pieces for Nomad's head and base, then molded and cast them in resin. The top antenna was made from wooden dowels and sheet acrylic.